
Premier's Awards of Design Excellence, Award of Merit for Architecture (2015)
Streamlined design.
The new air terminal building is a major component of the Winnipeg James Armstrong Richardson International Airport's redevelopment project. The 22-gate, two-level terminal and four-level parking garage replaces the existing terminal servicing international and domestic clients.
The new terminal building met the requirements for the commercial building incentive program (CBIP) and LEED. It was also the first airport in Canada, and the second in North America, to receive a LEED-certified rating.
Smith + Andersen designed the mechanical systems in a joint venture with SMS Engineering and TMP, utilizing our vast knowledge base of other airport projects to streamline the mechanical design into the architecture.
Streamlined design.
The new air terminal building is a major component of the Winnipeg James Armstrong Richardson International Airport's redevelopment project. The 22-gate, two-level terminal and four-level parking garage replaces the existing terminal servicing international and domestic clients.
The new terminal building met the requirements for the commercial building incentive program (CBIP) and LEED. It was also the first airport in Canada, and the second in North America, to receive a LEED-certified rating.
Smith + Andersen designed the mechanical systems in a joint venture with SMS Engineering and TMP, utilizing our vast knowledge base of other airport projects to streamline the mechanical design into the architecture.
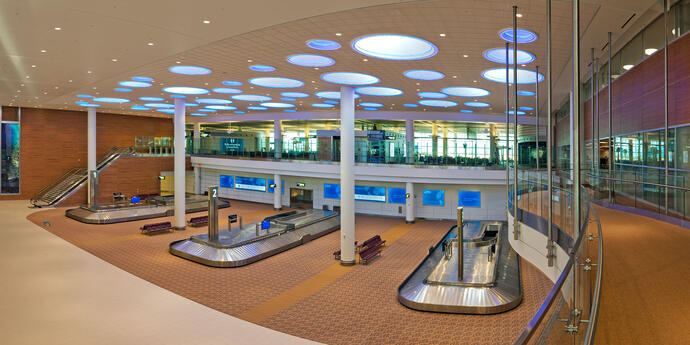
A runway success.
The mechanical systems include a combination of variable air volume and constant air volume systems with glycol heat recovery on exhaust air systems, waste heat recovery from heat pumps for utilization in low-temperature heating water systems, and in-slab hydronic radiant floor heating and cooling systems.
High-temperature heating water and chilled water is generated in the central utilities building (CUB) and is received by the new terminal for distribution. The heating water is cascaded to maximize the temperature difference and is returned to the CUB at a low temperature to maximize plant efficiency.
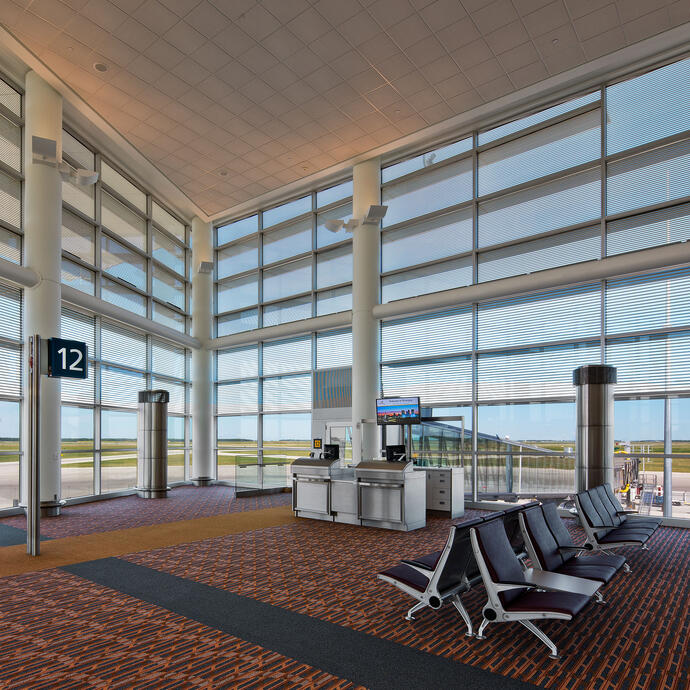
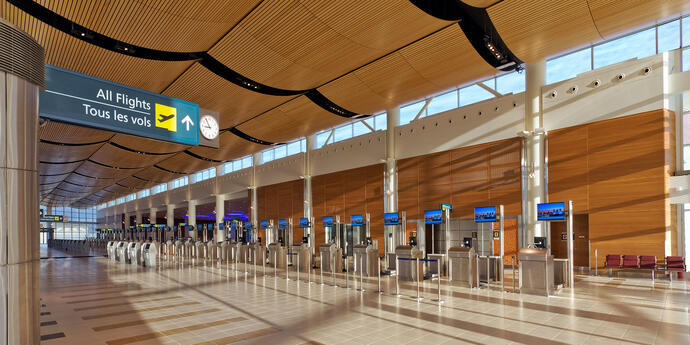